To optimize your race car’s performance, focus on understanding the key principles of aerodynamics. Utilize components such as spoilers, wings, and diffusers to enhance downforce while minimizing drag. Positioning these elements correctly can significantly influence your vehicle’s stability and speed on the track.
Pay attention to airflow management around your car’s body. Streamlined shapes reduce turbulence, allowing smoother movement through the air. Consider the placement of side skirts and underbody panels to improve airflow and decrease lift. A flat underbody design often proves beneficial in maintaining ground clearance and enhancing downforce.
Conducting wind tunnel tests is invaluable. These tests provide insights into the aerodynamic efficiency of your design, helping you make necessary adjustments before hitting the track. Analyze the data meticulously to fine-tune the balance between downforce and drag, adjusting angles and dimensions to achieve the desired aerodynamic profile.
Embrace the significance of active aerodynamics as well. Technologies like adjustable wings and movable diffusers can adapt during a race, optimizing performance based on real-time conditions. By implementing these strategies, you push the boundaries of speed and control, ensuring your race car remains competitive throughout the event.
Understanding Drag and Lift in Race Cars
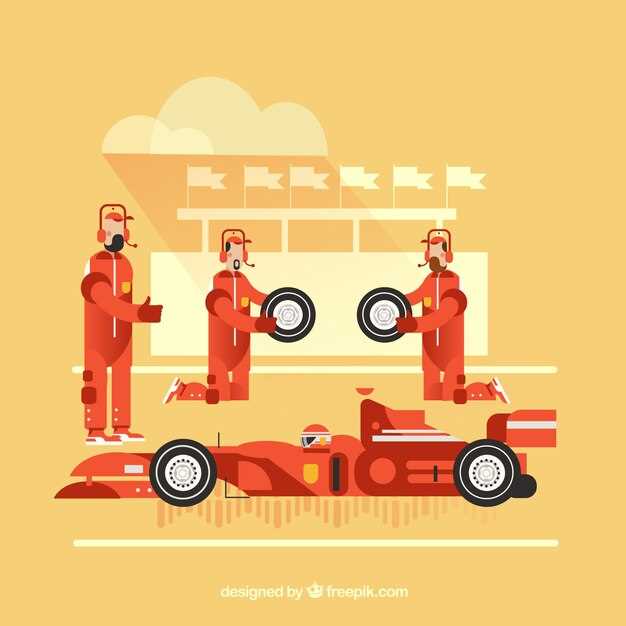
Optimize the aerodynamic design of a race car to effectively manage drag and lift. Minimizing drag, the resistance a car faces from air, enhances speed and fuel efficiency. Aim for a streamlined shape, reducing the frontal area. Incorporating features like smooth body contours and tapered rear sections can significantly decrease drag coefficient.
Implement active aerodynamics systems that adjust in real-time based on speed and track conditions. These systems can raise or lower certain components, such as spoilers, to adapt lift and drag forces dynamically, improving performance and stability at various speeds.
Drag Reduction Techniques
Focus on components such as air dams and underbody panels. These elements work to guide airflow around the car, minimizing turbulence. Keep in mind that every inch counts; small gaps or protrusions can lead to increased drag. Electronic data systems can monitor airflow in real-time, providing insights for ongoing adjustments.
Managing Lift for Better Handling
Utilize downforce to counteract lift, improving tire grip and handling. Spoilers and wings generate downforce by altering airflow, creating a pressurized difference above and below the car. Position these elements strategically to maximize their effectiveness without introducing excessive drag. Testing different angles and heights in a wind tunnel can yield valuable data for optimal configuration.
Optimizing Airflow Around Race Car Designs
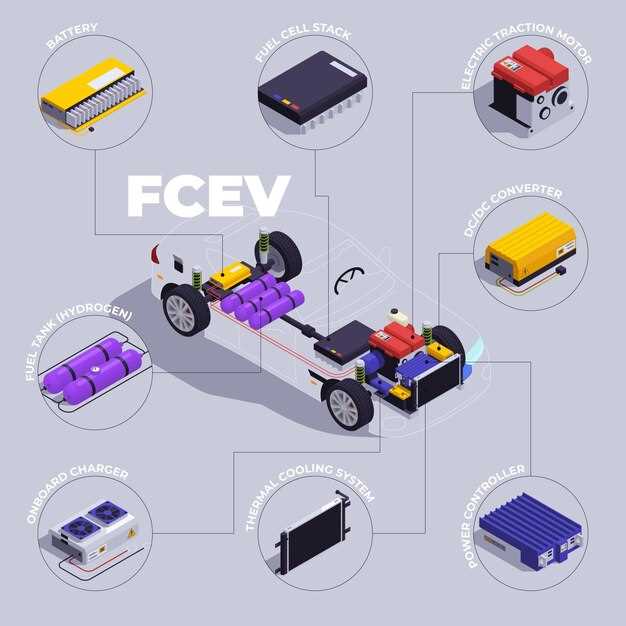
Refine the body shape to improve airflow. Streamlined silhouettes minimize drag and enhance downforce. Focus on smooth contours and integrated components, such as mirrors and air intakes, to reduce turbulence.
Incorporate splitters and diffusers. These elements manipulate airflow around the car, directing air under and over the vehicle. Adjust the angle of attack on these components to optimize performance across various speeds.
Utilize computational fluid dynamics (CFD) software. Run simulations to visualize airflow patterns and identify areas of high drag. Adjust the car design based on insights gained from various simulations, ensuring prototype development is data-driven.
Analyze the placement of cooling vents. Position them strategically to enhance both aerodynamic efficiency and engine performance. Ensure airflow over radiators does not disrupt the overall aerodynamic profile.
Design Element | Impact on Aerodynamics |
---|---|
Splitters | Increase front downforce, reduce lift |
Diffusers | Create low-pressure areas, improve rear stability |
Spoilers | Manage airflow, enhance overall grip |
Air Intakes | Facilitate cooling, minimize drag |
Experiment with surface textures. Smooth finishes reduce skin friction, while textured surfaces can manage airflow better in some areas. Balance these aspects to maintain high performance across different race conditions.
Monitor real-time data during races. Adjustments to strategy based on airflow performance can make a difference in lap times. Leverage telemetry to analyze performance and tweak setups for optimal results.
The Role of Spoilers and Wings in Downforce
Spoilers and wings significantly increase downforce, enhancing grip and stability at high speeds. For optimal performance, position these components to maximize airflow and pressure differentials. Use adjustable wings to adapt to varying track conditions. The angle of attack plays a pivotal role; a greater angle yields more downforce, but beware of increased drag.
Spoilers, placed on the rear of the vehicle, disrupt airflow and create turbulence, which reduces lift. This design helps maintain traction, especially during cornering. Consider a rear spoiler that complements your car’s design for balance, preventing unwanted lift during critical maneuvers.
Wings, often larger and more adjustable than spoilers, generate downforce through lift principles akin to aircraft wings. Front and rear wings must be carefully calibrated to ensure they work together. Fine-tune the camber angles to optimize aerodynamic characteristics based on track layout and driver preference.
Experiment with materials such as carbon fiber for lightweight and durable wings. An effective combination of spoiler and wing designs can enhance downforce while minimizing drag, leading to faster lap times and improved handling. Regular testing and refinement based on data and feedback from the track guarantee that your setup remains competitive.
Don’t overlook the importance of cleanliness. Any debris or damage can hinder airflow, reducing effectiveness. Ensure regular inspections and maintenance to keep the aerodynamics performing at their best. Overall, mastering the integration of spoilers and wings can turn your race car into a formidable competitor on the track.
Simulation Tools for Aerodynamic Analysis
Leverage Computational Fluid Dynamics (CFD) software for precise aerodynamic insights. Tools like ANSYS Fluent and OpenFOAM allow engineers to simulate airflow around race cars in various conditions. Start with ANSYS Fluent for its user-friendly interface and robust visualization capabilities. OpenFOAM, being open-source, offers flexibility for customization, making it a favorite among research-oriented teams.
Choosing the Right Tool
Select software based on your team’s needs and expertise. For beginners, Autodesk CFD provides straightforward simulations with basic functionalities. Those with advanced skills might opt for Siemens Star-CCM+, which combines CFD and multi-physics simulations. Compare simulation speed, mesh generation, and user support when making your decision.
Real-time Simulation and Testing
Consider real-time simulation tools like Race Engineer or MATLAB Simulink. These applications enable live data analysis during test sessions, allowing immediate adjustments to vehicle setup. Integrating sensor data with aerodynamic models enhances predictive capabilities, helping teams refine designs more rapidly.
Wind Tunnel Testing: Methods and Benefits
For accurate race car aerodynamics assessments, wind tunnel testing stands out as a critical practice. This method reveals how different designs interact with airflow, resulting in significant performance gains. Here are the primary methods and their benefits.
Static Testing
Static testing involves placing a stationary model in the wind tunnel. This allows engineers to measure forces acting on the vehicle at various angles. Key approaches include:
- Force Measurement: Utilize load cells to quantify lift, drag, and side forces, giving insights into overall aerodynamic efficiency.
- Surface Pressure Mapping: Employ pressure taps to collect data on pressure distribution across the body, identifying areas for improvement.
Dynamic Testing
Dynamic testing simulates real-life conditions by moving the model within the tunnel, providing a realistic representation of airflow. Techniques include:
- Moving Ground Simulation: Integrate a moving belt to replicate the ground effect, crucial for understanding downforce changes.
- Yaw and Roll Testing: Implement adjustable models to measure performance under various orientations, enhancing cornering behavior analysis.
Benefits of Wind Tunnel Testing
- Performance Optimization: Identify and refine aerodynamic features, leading to reduced drag and increased downforce.
- Cost Efficiency: Address design issues early in the process, minimizing expensive modifications during actual racetrack testing.
- Data-Driven Decisions: Utilize quantitative data to make informed design choices, ensuring optimal vehicle performance.
- Rapid Prototyping: Test multiple design iterations quickly, allowing for a faster development cycle.
Incorporating wind tunnel testing into the design process enhances both the speed and reliability of race cars, directly impacting their competitive edge on the track.
Real-World Applications of Computational Fluid Dynamics
Utilize Computational Fluid Dynamics (CFD) to enhance the performance of race cars through precise aerodynamic modeling. CFD allows engineers to simulate airflow around the car, optimizing designs for reduced drag and improved downforce. This process minimizes reliance on costly wind tunnel testing while providing detailed insights into fluid behavior at various speeds and angles.
Design Optimization
Incorporate CFD analysis during the early stages of car design. Create multiple design configurations to evaluate different aerodynamic profiles and components. For instance, analyze the impact of front spoilers, side skirts, and rear wings on aerodynamic efficiency. By leveraging simulation data, teams can refine shapes and materials, ultimately improving lap times and vehicle stability on the track.
Performance Enhancement
Apply CFD in real-time during race events. Monitor airflow and temperature around critical components, such as the engine and brakes, to prevent overheating and maintain optimal performance. Teams can adjust aerodynamics on-the-fly based on simulation forecasts, enhancing strategy and giving drivers a competitive edge. This adaptability plays a crucial role in high-stakes racing where milliseconds can determine victory.
Use CFD to explore innovative edge cases. Test boundary layer control devices, such as vortex generators or active aerodynamics, to achieve unparalleled performance. Experimenting with unconventional configurations can yield significant advantages, helping teams outpace competitors in the relentless pursuit of speed.
Balancing Aerodynamics and Weight Distribution
Adjust weight distribution to enhance your car’s cornering ability without compromising aerodynamic performance. Aim for a balanced setup that maintains stability through corners while reducing drag on straights.
Weight Distribution Strategies
- Place heavier components, like the engine and transmission, as low as possible in the chassis to lower the center of gravity.
- Position weight toward the rear to improve traction during acceleration, especially in rear-wheel drive setups.
- Use adjustable ballast to fine-tune weight distribution according to track conditions and vehicle handling characteristics.
Aerodynamic Considerations
- Smooth out airflow by using underbody panels and diffusers to minimize drag, allowing the car to cut through the air more efficiently.
- Optimize the shape of the front and rear wings for the specific track layout, ensuring they generate the required downforce without adding excessive weight.
- Test different ride heights to find the sweet spot where aerodynamics and handling harmonize, maintaining downforce without inducing drag.
Conduct thorough testing with weight changes and aerodynamic modifications to assess performance impacts. Data-driven decisions lead to better setups that maximize both speed and handling on the track.
Impact of Tire Design on Aerodynamic Performance
Tire design significantly influences aerodynamic efficiency, affecting the overall speed and stability of race cars. Choosing low-profile tires reduces sidewall flex, which minimizes turbulence and enhances grip. Opt for wider contact patches for better traction and improved airflow around the tires.
Tread patterns play a critical role in managing airflow. Smooth, limited tread reduces drag compared to aggressive patterns. Consider slick tires for optimal performance on dry tracks, as they enhance surface contact and streamline aerodynamics.
The sidewall construction, including materials used, alters the tire’s behavior under pressure. Stiffer compounds maintain shape at high speeds, reducing deformation that increases drag. Investing in advanced materials can yield lighter tires that contribute to improved lap times and better fuel efficiency.
Aerodynamic wheel designs also complement tire performance. Spoke configurations should favor solid designs that channel airflow efficiently. Closed or covered wheels can minimize turbulence and enhance the car’s overall aerodynamic profile.
Keep in mind the balance between tire pressure and performance. Higher pressures lower contact area, which may reduce rolling resistance but can compromise grip. Monitor tire temperatures to find the optimal pressure settings for specific track conditions.
Incorporating aerodynamic enhancements like wheel fairings can further optimize airflow around tires, reducing drag. These modifications help maintain stability at high speeds, leading to improved performance on the track.
Regularly evaluate tire performance through data analysis during test runs. Pay attention to how changes in design or pressure affect handling and speed. By prioritizing aerodynamic characteristics in tire design, teams can achieve competitive advantages in racing events.
Adjustable Aerodynamics: Wings and Body Kits
Install adjustable wings to enhance downforce and optimize the car’s stability. Fixed wings provide a one-size-fits-all approach, limiting performance during different racing conditions. Adjustable wings allow for real-time tuning, enabling drivers to adapt based on track characteristics–more downforce on tight corners and reduced drag on straights.
Consider using a multi-element wing design for increased aerodynamic efficiency. This setup can be fine-tuned to balance downforce and drag, improving overall lap times. Make sure to adjust the angle of attack; small adjustments can lead to significant changes in performance.
Body kits complement adjustable wings by improving airflow around the vehicle. Look for kits designed with canards or splitters that redirect airflow to reduce turbulence and enhance grip. These modifications not only increase downforce but also give a competitive edge by optimizing the vehicle’s aerodynamics at different speeds.
Integrate adjustable rear diffusers for additional aerodynamic benefits. These can be altered based on racing conditions and provide increased downforce without a proportional increase in drag. Experiment with various configurations during practice sessions to find the ideal setup for each track.
Regularly assess wing and body kit performance through data logging and telemetry. Track changes in downforce, drag, and overall vehicle behavior under various conditions. Fine-tune settings based on collected data to ensure maximum effectiveness, and keep refining the setup for continued improvement.
Learning from Historical Aerodynamic Innovations in Motorsport
Examine the early innovations in aerodynamics within motorsport to harness valuable insights for contemporary designs. The streamlined shapes of the 1930s Mercedes Benz W25 and Auto Union cars set a foundation, demonstrating that smooth surfaces can significantly reduce drag. Aim for clean lines and minimized turbulence in your designs, as these characteristics proved effective in achieving high speeds.
The Importance of Downforce
Consider the innovations from the 1960s that introduced the concept of downforce. The Wing design on the Lotus 49 was revolutionary, providing increased grip and stability. Today’s race cars should incorporate adjustable aerodynamics, allowing teams to optimize downforce for varying track conditions.
- Experiment with front and rear wings to find the ideal balance.
- Use computational fluid dynamics (CFD) to predict airflow patterns.
- Integrate ground effect principles for enhanced cornering performance.
Explore the progress in materials since the 1970s when lightweight components became critical. The use of carbon fiber and composites allows for robust, lightweight structures, improving overall performance. Focus on weight reduction while maintaining durability and safety standards.
- Utilize advanced simulation tools to test material strengths.
- Incorporate lessons from the past, such as the success of the McLaren MP4/1.
- Iterate designs based on real-world testing in different racing environments.
History provides a roadmap for current engineers and designers, highlighting which aerodynamic strategies have stood the test of time. By adopting these historical lessons, you can pave the way for future innovations in race car aerodynamics.
Future Trends in Race Car Aerodynamic Technology
Advancements in computational fluid dynamics (CFD) allow engineers to simulate airflow with unprecedented accuracy. This technology minimizes the need for physical wind tunnel testing, saving time and resources while facilitating rapid design iterations. Embracing real-time data analysis during races enhances adaptive strategies for downforce adjustment based on track conditions. Teams increasingly rely on telemetry to analyze aerodynamic efficiency as races unfold.
Active Aerodynamics
Active aerodynamic systems are becoming commonplace, allowing for dynamic adjustments based on speed and driving conditions. These systems include movable wings and adjustable diffusers. By altering the aerodynamic profile in real-time, race cars can optimize downforce during cornering and reduce drag on straightaways. Adoption of lightweight materials enhances these systems’ efficiency without compromising structural integrity.
Artificial Intelligence Integration
Integrating artificial intelligence into aerodynamic design tools significantly enhances predictive modeling. AI algorithms analyze vast datasets from previous races to identify patterns and optimize design choices. This technology assists engineers in predicting how aerodynamic changes will perform under various scenarios and streamlines the development process. As AI continues to advance, the accuracy of aerodynamic simulations will improve, leading to faster and more effective design cycles.
Trend | Description | Impact |
---|---|---|
Computational Fluid Dynamics (CFD) | Enhanced simulations minimizing wind tunnel testing. | Faster design iterations and increased accuracy. |
Active Aerodynamics | Dynamic adjustment of aerodynamic components during races. | Improved performance across varying conditions. |
Artificial Intelligence | Use of AI for predictive modeling and design optimization. | Increased efficiency in design cycles and performance analytics. |
Lightweight Materials | Innovations in materials reduce weight in active systems. | Enhanced performance without structural compromise. |
Collaborations between car manufacturers and technology firms push these trends forward. Investing in these innovative technologies positions teams for greater success in competitive environments. Adapting to these emerging trends will remain key as the quest for speed and efficiency continues.
Challenges in Implementing Aerodynamic Solutions on Track
Testing and validating aerodynamic solutions require precise data collection from various sensors installed on race cars. Implement real-time telemetry systems to capture airflow patterns and downforce levels during laps. This will help refine designs and quickly address issues.
Balancing aerodynamic efficiency with mechanical grip often presents a challenge. Adjust suspension settings in tandem with aerodynamic tweaks to maintain optimal tire contact with the track. This ensures that downforce translates into performance rather than drag.
Weather conditions greatly influence aerodynamic performance. Implement adjustable aerodynamic components, such as front splitters and rear wings, to adapt to changing air density and wind direction. This flexibility allows teams to optimize their setups for varying track conditions.
Cost constraints limit the extent to which teams can experiment with advanced aerodynamic features. Prioritize testing of the most impactful solutions and consider simulations to reduce physical resource use. Invest in computational fluid dynamics (CFD) to identify areas for improvement without extensive wind tunnel testing.
Driver feedback plays a critical role in fine-tuning aerodynamic performance. Encourage open communication between drivers and engineers to gather insights on handling and stability. This collaboration enables quicker adjustments to enhance overall racing performance.
Regulatory restrictions can hinder the implementation of cutting-edge aerodynamic features. Stay informed about sanctioning body rules to ensure compliance while pushing the boundaries of design innovation. Engage with technical committees to advocate for regulations that foster development without compromising safety.
Finally, the track’s layout impacts design choices. Analyze specific circuit characteristics, such as long straights and tight corners, to tailor aerodynamic packages that maximize performance for each event. This targeted approach addresses unique challenges and leverages the car’s strengths effectively.
Video:
How aerodynamics help make a car go faster
How aerodynamics help make a car go faster by Interesting Engineering 261,063 views 4 years ago 5 minutes, 10 seconds
Q&A:
What are the basic principles of race car aerodynamics?
The basic principles of race car aerodynamics revolve around the concepts of downforce, drag, and airflow. Downforce is the force that pushes the car down onto the track, which increases traction and helps in cornering. This is primarily achieved through the shape of the car and the addition of wings or other aerodynamic elements. Drag, on the other hand, is the resistance the car faces as it moves through the air, and reducing drag is crucial for increasing speed. Effective aerodynamics balances these two forces, allowing a race car to maintain high speeds while maximizing control and stability on the track.
How does the shape of a race car influence its aerodynamic performance?
The shape of a race car plays a significant role in its aerodynamic performance. Streamlined designs that minimize air resistance allow the car to cut through the air more efficiently. This involves smooth, curvilinear surfaces and features that guide airflow, such as flat floors and spoilers. A well-designed shape reduces drag, allowing the car to achieve higher speeds. Conversely, adding elements like wings can increase downforce, enhancing grip during high-speed maneuvers. The balance between reducing drag and maximizing downforce is critical for achieving optimal performance on the track.
What are some common aerodynamic features found on race cars?
Race cars often incorporate several aerodynamic features designed to enhance performance. Some common features include front and rear wings, which create downforce and help stabilize the vehicle at high speeds. Splitters and diffusers are used at the front and rear, respectively, to manage airflow around the car. Vortex generators may be added to improve air separation and reduce drag. Additionally, the use of underbody aerodynamics, such as a flat floor or ground effects, can further enhance downforce without significantly increasing drag. Each of these features is carefully engineered to optimize the car’s performance concerning its weight and speed.
How do teams test and refine aerodynamic designs?
Teams utilize various methods to test and refine their aerodynamic designs. One common approach is using wind tunnel testing, where scale models of the car are subjected to controlled airflow conditions to study the effects of different shapes and components on drag and downforce. Computational fluid dynamics (CFD) is another advanced method that employs simulations to analyze airflow around the car. Data from actual track testing is also invaluable, as teams gather performance metrics to assess the effectiveness of their designs under real racing conditions. By combining these methods, teams can iteratively improve their car’s aerodynamics for optimal performance.